- Nutro Inc.
- Automation
Nutro inc. Automation
Nutro Inc. Process Automation
Nutro builds virtually hands-off systems from beginning to end. Robotic material handling and vision systems guide the loading and unloading of each part. This leads to an increase in production, saves on labor cost, and makes for a fully automated system from beginning to end. With the help of Nutro, you can optimize your current process with modern automation solutions. Our systems can convey, rotate, and turn parts.
The following design parameters are achieved with Nutro automation:
Process control - programmable controls of the painting parameters including fluid pressure, fan spray pattern, atomizing air, and distance from spray gun to product.
Productivity - labor reduction and increased throughput.
Quality - high quality parts with minimal variation are consistently produced.
Cost savings - costs are reduced by minimizing overspray, decreasing reject rates and eliminating many operator- related issues.
Environment - operators are removed from the spray booth environment, reducing health and safety issues.
If you are looking for flat line belt or chain system to transport your parts please go to the experts, our parent company, Venjakob.
Conveyance:
Nutro has a multitude of different options for conveyance. Nutro engineers will develop the best method in transporting your product through the finishing system. We have manufactured: Chain on edge, over head, over head power and free, inverted monorail, chain driven live roller, belt, and over under. These are just a few of the conveyance options Nutro can provide to best suit your companies needs.
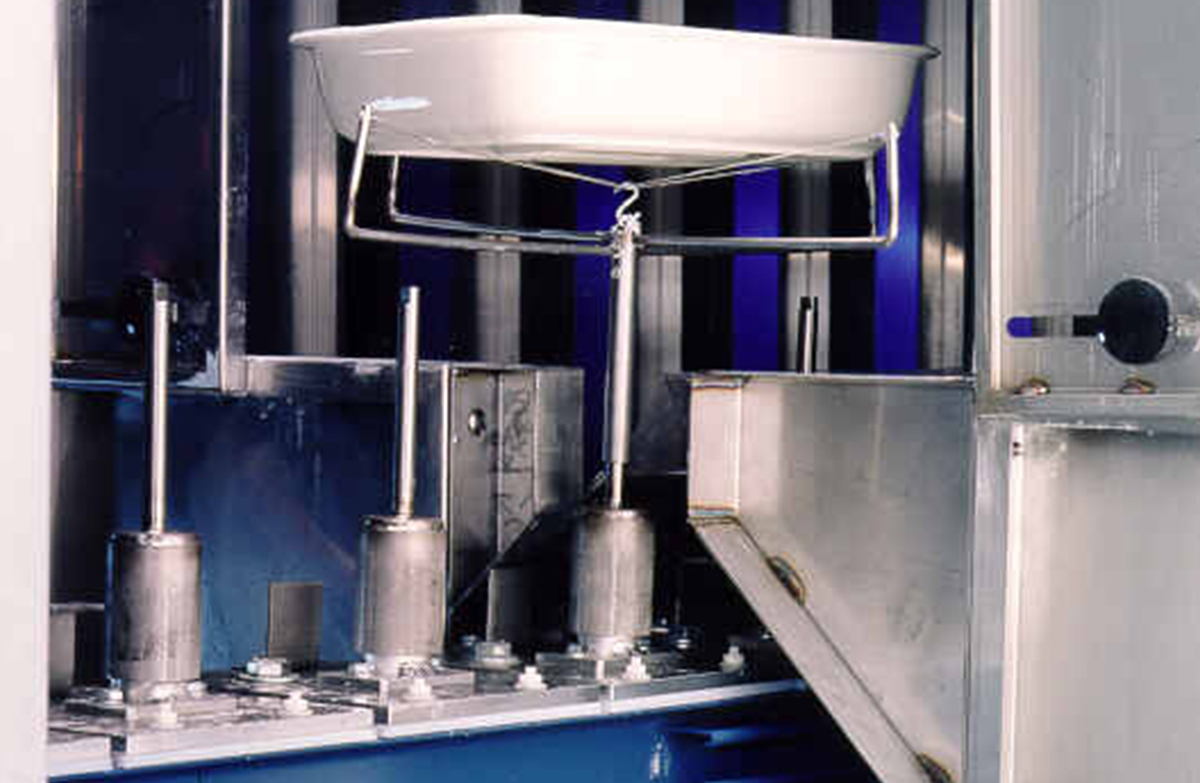
- Overhead Conveyors- Low initial cost, hanging flexibility, ability to make horizontal and vertical curves.
- Overhead Power & Free- Additional flexibility via their ability to switch carriers in and out of powered loops, accumulate carriers on free rails for offline work or to achieve diagonal parking for better parts density in ovens.
- Inverted Monorail- Place the conveyor chain and tracks below the carrier and product to reduce contamination.
- Flat Belt- Have the potential to carry a wide range of products without the need for custom fixturing.
- Over/Under Fixture Conveyors- provide the possibility of handling products in a more precise manner than the above methods. Limited to straight line layouts.
- Chain On Edge- Offer the precise handling capabilities of the over/under fixture conveyor plus many other possibilities. Every foot of the conveyor chain can be used for process and layouts of any shape and size can be constructed from standardized modules.
From Small Spray Machines to Custom- Nutro’s Chain-On-Edge Delivers
The Conveyor- The heart of the system, designed to be trouble free and easy running, has variable part spacing to provide the most economical “pack” for your application.
Conveyor Shrouds- made of durable stainless steel, they protect the conveyor chain and spinner belts from overspray throughout the booth.
Work holders- Designed especially for your product can be furnished. Even more practical, a universal holder to handle a variety of sizes or shapes can be developed for you.
Nutro combines the most efficient spray method with precise and controlled handling to deliver outstanding results for you. Nutro’s automatic spray machines reduce rejects, improve safety and cleanliness, and save on expensive “compliance” coatings.
There is no universal best choice of conveyor style for all finishing applications. The key factors that must be considered when making this decision include:
- What are the shapes and sizes of the parts to be finished?
- How can the parts be fixtured?
- What type of pretreatment process is needed?
- Will a transfer between pretreatment and finishing be necessary?
- What degree of finish quality is needed?
- Should the part be rotated, oriented, or masked?
- What type of curing will be employed?
- Will the process benefit from further automation?
Robot material handling:
The following design parameters are achieved using a robot:
- Process control- programmable controls of the painting parameters including fluid pressure, fan spray pattern, atomizing air, and distance from spray gun to rotor.
- Productivity- labor reduction and increased throughput.
- Quality- high quality parts with minimal variation are consistently produced.
- Contouring- with six-axis flexibility and advanced control software that automatically recognizes any of the three robots being processed, complex contouring is easily achievable.
- Cost savings- costs are reduced by minimizing overspray, decreasing reject rates and eliminating many operator related issues.
- Environment- operators are removed from the spray booth environment, reducing health and safety issues.
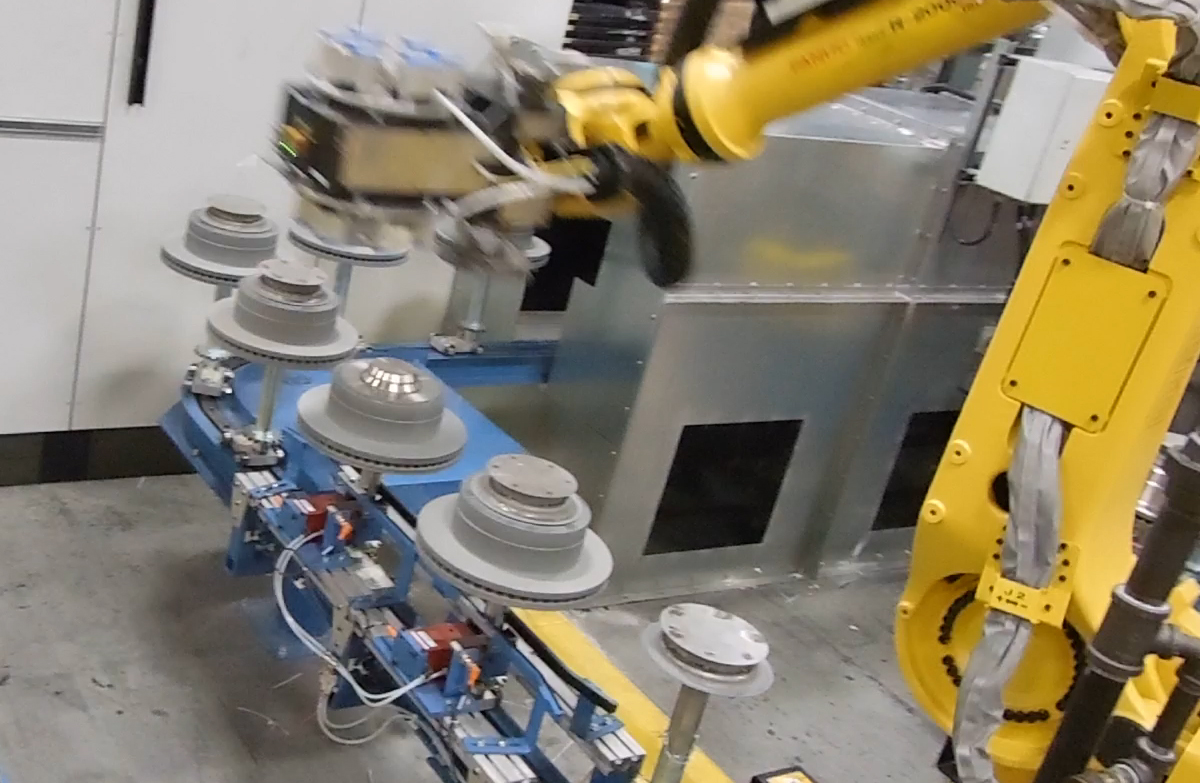
A foundation to Nutro Inc’s fully automated systems is our robotic integration. An example of one of our fully automated robotic systems is as follows: An outstanding capacity of 300 parts per hour includes pallet unloading, induction heating, twin robotic spray, inspection, drying, unloading and spindle cleaning for low maintenance. In its entirety, the system occupies a minimal amount of plant floor space and requires operators only to supervise the process. Each part is preloaded into the system’s programmed controller and can be immediately recalled.
Our experts would love to show you how to optimize your current machinery. If you would like to find out more information, please contact us.